It’s the beginning of December and on my usual Craigslist searches, I happen to find “the machine” I wanted. A larger sized lathe than I already had, with a quick change gear box, and a bonus: an American-made quick change tool post. (Not cheap!) Complete lathe package but with no tooling, asking price? $1750. Seems a little high and I have no money, what can I do? I contact the seller, Pete, and ask my questions, and ask if he might be willing to hold it for me for a bit. It seemed too easy, but he was happy to do so AND come down in price. Long story short, I sold my 1962 Craftsman 101.21400 metal lathe and a pair of Sherline machines (lathe and mill) that I had bought earlier in the year. My intention with the Sherline machines (micro sized) was to have milling capabilities. It was simply too small, but fit nicely in the shop. I figured I’d rather get a better lathe for my everyday (okay, every week) work and a milling attachment. (More on that later.)
I sold the Craftsman lathe and Sherline package for a little less than my asking price but plenty enough to cover my costs of the “new” lathe and some rentals/straps costs, etc. Made a new friend in the process, Cole, who runs a business modifying atomizers for smokers. It’s nice to sell the lathe to someone close by who I know will actually use it!
Everything is sold, space is in the shop, money in the pocket… time to rent a trailer! I find a great “drop deck” trailer from Sun Belt Rental pretty close to my home and reserve it online on a Saturday night. They open Monday morning…
In my mind the few days leading up to this move, I prepared many things:
* Find a used trailer hitch and install it on my van
* Wire said trailer hitch for lights – maybe a post about that adventure later…
* Find rental trailer
* Study other people’s online posts about moving machinery
* Buy various things like tarps, tie-downs, and 2×4 skids
* Plan a route into the actual workshop, which had me thinking about replacing the doorway with something bigger and without threshold
* Clear workshop space out (6’x12′ area leaves NO space for anything to be in the way when moving in)
On December 8th, a cold and windy Monday morning, I get a call at 7:15am from the rental company I had reserved a “drop deck” trailer from to go from Greenville, SC up to Canton, NC to meet Pete and buy the metal lathe. The company doesn’t have my trailer! Not good. Luckily U-Haul always has something ready for rental, even if it’s not as nice of a trailer that drops the floor to ground level so you can roll stuff in.
I tried in vain to find another company at 7:45 in the morning that has a trailer I could rent and eventually gave up and went back to U-Haul. But that deal was pretty smooth – less than $40 and I’m out the door, hooked to a 9×5′ ramped trailer with my recently installed trailer hitch on the “Dan Van,” otherwise known as a 2001 Honda Odyssey.
I head up a hill into the neighborhood to pick up Tim, the machine shop owner and machinist who has helped me with making the custom chain timpani parts for my kits. Tim agreed to go with me and lend not only his machining experience in evaluating the lathe, but also moving it, which was no small feat and deserves this post dedicated to the task. Tim throws some ratcheting straps, come-alongs, rolling pipes, 2x4s and some floor jacks into the trailer and we headed out for Canton, NC, up a steep hill known as the “Saluda Grade.”
The trip up the grade was smooth but burned some gas hauling the trailer. It took about 110 minutes when Google Maps said it should take less than 90. Slow and steady wins this (non) race and gets everybody home safe! Pulling off the interstate and into the wooded area that Pete, the previous owner, lived was when the adventure really began. Going up mountain roads, my imagination was seeing a trailer tumble down a hill sideways. Then we hit gravel…
Pulling into Pete’s driveway was an incredible task. Loose gravel and a steep slope made it impossible to do without skidding around a little with a running start. I had to back out and try twice before getting up the hill and into the flat area (on top of a mountain) that was Pete’s driveway.
When we finally were parked in front of Pete’s shop, we were greeted with this view:
I didn’t take any photos of the actual loading (I was busy) but it went rather smoothly. Pete, Tim and I used some rolling dollies (which Pete was kind enough to let me keep) to roll the lathe out of his shop and onto the plywood covered ramp to the trailer. Tim hooked up a come-along and we ratcheted the whole thing onto some 2x4s sitting in the bed of the trailer. Once centered in the trailer and on the 2x4s, I drove some lag screws into the wood and we collectively strapped the lathe in as many ways as we could. Knowing the drive we had ahead of us, I wanted this thing attached tight.
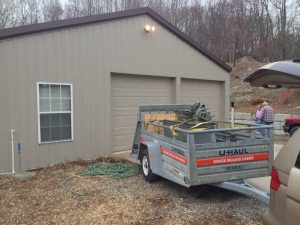
Tim and Pete had some nice conversation about their shops and what they both did a living, while I snapped some photos and cleaned up a little bit. Pete mentioned to us a scrap yard, Biltmore Iron and Metal, which we decided we would pay a visit to on the way back down the hill to Greenville. The plan was to find possibly some 3 phase motors (for my VFD project) or machinery parts to help setup the “new” lathe. We had no luck.
The trip back home went smoothly after a stop for a late lunch. We had a little rain which concerned me for two reasons: rust and slippery roads. Neither problem presented itself.
I’ll detail the unloading and installing the lathe in another post, this one is already too long! Honestly, most people wouldn’t care to read this far, and would rather me just say, “things went well and nobody died.” But if you read this far, you’re likely one of the few people actually interested in how this all worked out. That post will be titled “Putting Down” ….More later.
DK
Leave a Reply